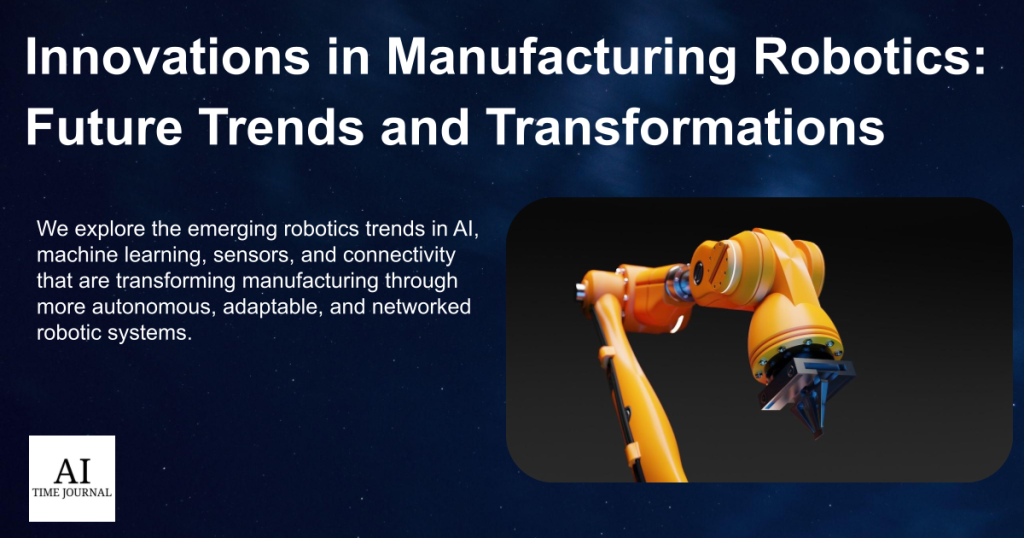
Future robotics traits may have a profound affect on many industries and reshape the basics of manufacturing processes within the ever-changing dynamic panorama of recent manufacturing. On the forefront of this revolutionary wave that’s bringing in a brand new period by the convergence of innovation and know-how are producers. The importance of adopting these rising traits is explored in depth on this piece. As we navigate by the intricate realm of producing robotics, understanding the evolving definition of what it means to be a producer turns into crucial.
The time period “manufacturer” extends past standard boundaries, encapsulating those that harness cutting-edge robotics to drive effectivity and redefine manufacturing requirements. Moreover, an insightful overview of key improvements turns into our information, illuminating the trail towards a future the place robotics performs a pivotal position in defining the panorama of producing. Be a part of us on this exploration as we unravel the transformative journey of producing robotics and its profound implications for the long run.
Desk of Contents
AI and Machine Studying Integration
An age of elevated effectivity and suppleness on the manufacturing facility ground is being ushered in by the mixture of Artificial Intelligence (AI) and Machine Learning (ML) within the dynamic discipline of producing robotics. The numerous contribution AI has made to enhancing the capabilities of producing robots lies on the coronary heart of this development. AI offers robotic techniques with subtle algorithms that allow extra advanced sensing, studying, and decision-making, in the end resulting in elevated autonomy of those machines. AI-driven robotics exhibit a stunning diploma of accuracy and effectivity in a wide range of jobs, from sophisticated high quality management procedures to tough meeting duties.
Machine Studying is essential on this course of that takes the adaptability of robots to unprecedented ranges. Robots with machine studying algorithms are all the time enhancing their efficiency by publicity to varied duties and settings. This flexibility permits robots to simply combine into completely different processes with no need for reprogramming, which is essential in dynamic manufacturing conditions the place duties might change.
In manufacturing, using AI-driven predictive upkeep is changing into important. These AI algorithms put in place make the most of sensor knowledge and previous efficiency to forecast doable issues and recommend preventive upkeep actions. This reduces downtime and maximizes the longevity and general effectivity of robotic techniques, making them extra reliable members of the manufacturing ecosystem.
Right here we will now Delve into some real-world functions, and case research that provide tangible insights into the transformative affect of AI-enhanced robotics. The corporate we can be looking into is Siemens they’re a know-how firm with a concentrate on transportation, infrastructure, trade, and healthcare. They lead the worldwide marketplace for industrial automation and industrial software program and are the most important industrial manufacturing agency in Europe.
We discovered that:
- Siemens is using AI-enhanced robotics to enhance the general job efficiency of their machines.
- The robots’ performance hinges on the accuracy of their controllers to trace predefined motions, which is why this firm’s key focus is on automation to get the method down completely.
- Siemens is giving machines larger intelligence to allow them to be taught on their very own and generalize about circumstances they haven’t skilled could be revolutionary for a lot of completely different industries.
IoT and Trade 4.0
The Internet of Things (IoT) and Industry 4.0, when mixed, are proving to be a transformative pressure within the quickly altering discipline of producing robotics, redefining the elemental construction of commercial processes. At its core, IoT includes connecting units and techniques to collect and change knowledge. Within the context of Trade 4.0, sometimes called IoT 4.0, this connectivity extends to an unprecedented scale. In manufacturing, IoT facilitates the creation of a digital thread, interlinking each side of the manufacturing course of, from equipment to produce chains. This interconnectedness lays the inspiration for a sensible and responsive manufacturing ecosystem.
Trade 4.0 stands on 4 pillars:
- Connectivity
- Knowledge transparency
- Technical help
- Decentralized decision-making.
The convergence of those pillars kinds the spine of a cyber-physical system the place IoT allows seamless communication between machines, workpieces, and human operators. This interconnectedness fosters real-time monitoring, data-driven decision-making, and a holistic view of the whole manufacturing panorama.
When manufacturing robotics, the synergy between IoT and robots is a game-changer. Robots geared up with IoT sensors can talk with one another and with different linked units within the manufacturing surroundings. This real-time knowledge change facilitates a holistic view of the manufacturing course of, enabling robots to align their actions with the broader goals of the manufacturing system. Together with this, one other side of this synergy is how robots geared up with sensors can determine the presence of different equipment or human staff and react accordingly. At this stage of cooperation, security is improved, and robots can successfully collaborate with people. To scale back the possibility of accidents, a robotic outfitted with Web of Issues sensors, as an illustration, can change course or velocity in response to the presence of human staff.
The mixing of Trade 4.0 and IoT in robotics manufacturing gives vital benefits. Listed here are a couple of situations of each the benefits and the challenges that include them:
Advantages of IoT in Manufacturing
- Enhanced Operational Effectivity – Actual-time monitoring and knowledge analytics will optimize manufacturing processes. Predictive upkeep lowers downtime by addressing main points earlier than they trigger disruptions.
- Improved Choice-Making – Knowledge-driven insights allow knowledgeable and strategic decision-making. Analytics on manufacturing metrics improve agility and responsiveness to altering calls for.
- Collaborative Work Environments- Permits collaborative robotics, fostering a safer and extra environment friendly working surroundings. Human-robot collaboration enhances productiveness and suppleness in manufacturing duties.
Challenges of IoT in Manufacturing
- Safety Issues – Elevated connectivity creates potential vulnerabilities for cyberattacks. Making certain strong cybersecurity measures is pivotal to guarding delicate knowledge.
- Price of Implementation – The preliminary funding in IoT infrastructure and know-how might be substantial. Lengthy-term advantages have to justify the upfront prices for widespread adoption.
- Scalability Challenges – Scaling IoT options to accommodate rising manufacturing operations might be difficult. Planning for future scalability is essential to keep away from disruptions because the enterprise expands. Navigating these challenges whereas harnessing the advantages of IoT is pivotal for producers aiming to leverage the transformative potential of interconnected applied sciences.
Superior Sensors and Imaginative and prescient Techniques
Sensors are important in robotics; they’re like sensory organs that assist robots understand and work together with their environment. Their advanced features embody environmental notion, which helps robots make sense of their environment by measuring parts like strain, humidity, and temperature. Moreover, sensors help vital operations like as object detection and localization, which allow robots to determine and find objects with accuracy. This can be a fundamental perform in a wide range of functions, from manufacturing to autonomous navigation. Moreover, sensors give management techniques real-time enter, leading to a closed-loop system that improves robotic actions’ accuracy and responsiveness.
Additionally, when working with superior sensors, varied varieties serve distinct features. LiDAR, using laser mild for exact distance measurement, finds functions in mapping and navigation. Pressure/torque sensors measure utilized pressure and torque, essential for duties demanding delicate contact and pressure management. Inertial Measurement Models (IMUs), combining accelerometers and gyroscopes, guarantee steadiness/stability in cell robots. Imaginative and prescient sensors, together with cameras with superior options like depth notion, seize visible knowledge for picture processing and recognition.
Now shifting on to imaginative and prescient techniques, that are a subset of superior sensors, that emulate human-like visible notion in robots. These techniques leverage cameras in addition to picture processing to seize and interpret visible knowledge, enabling the robots to acknowledge and monitor objects in actual time. Imaginative and prescient algorithms additionally improve picture interpretation, contributing to strong decision-making. Furthermore, superior cameras with depth-sensing applied sciences present 3D notion, facilitating enhanced spatial understanding.
In functions, the mixing of those superior sensors and imaginative and prescient techniques heralds transformative adjustments; under are the applying benefits:
- Sensors and imaginative and prescient techniques optimize manufacturing processes for elevated effectivity.
- LiDAR and vision systems play a pivotal position within the navigation of autonomous autos. Which Permits real-time mapping, impediment detection, and path planning.
- Force torque sensors contribute to the fragile duties carried out by medical robots in addition to imaginative and prescient techniques aid in surgeries, diagnostics, patient care, and more.
- Harvesting and crop monitoring are made simpler by imaginative and prescient techniques. Using sensors maximizes using assets in sustainable agriculture.
Robotics in SMEs (Small and Medium-sized Enterprises)
The mixing of robotics in Small and Medium-sized Enterprises (SMEs) is a compelling side of the evolving manufacturing panorama, albeit accompanied by distinctive challenges. SMEs usually face constraints resembling restricted monetary assets and the necessity for versatile, simply deployable options. The challenges prolong to the experience required for the implementation of advanced robotic techniques. Nevertheless, the long run holds promising developments to deal with these obstacles.
Price-effective options emerge as a key consideration for SMEs venturing into robotics. Improvements in robotic applied sciences purpose to supply reasonably priced and scalable choices tailor-made to the precise wants of smaller enterprises. This contains modular robotic techniques that may be simply built-in into current workflows, minimizing disruption and offering a phased strategy to automation.
Collaborative robotics, characterised by robots working alongside human counterparts, presents an intriguing avenue for SMEs. These robots are designed to be inherently protected and adaptable, permitting for shut collaboration with out the necessity for intensive security measures. This collaborative strategy enhances flexibility in duties, making it appropriate for dynamic SME environments the place manufacturing necessities might fluctuate.
Due to developments in collaborative robotics, producers at the moment are capable of implement automation in exactly outlined areas, opening up alternatives for SMEs. The state of affairs involving Mississauga-based audio producer Paradigm Electronics is an ideal illustration of this. The corporate unveiled a speaker cupboard with a lacquer end that wanted lots of sanding and sprucing along with a number of coats of end. On account of an absence of certified personnel, they employed Superior Movement & Controls to deploy a collaborative robotic from Universal Robotics (UR) that will work alongside a professional operator. This undertaking, accomplished in slightly greater than a month, produced a 14-month return on investment and enhanced the cell’s throughput by 50%.
Robotics in Hazardous Environments
Two noteworthy sectors the place robotics is making vital strides are the Nuclear Trade and the Chemical and Pharmaceutical Trade. First off, the nuclear trade depends on robotics to navigate environments saturated with radiation, guaranteeing the protection of each operations and employees. Robots geared up with superior sensors and precision instruments undertake duties resembling inspection, upkeep, and dealing with of radioactive supplies. By minimizing human publicity to hazardous circumstances, these robots contribute to the reliability and security of nuclear operations.
Subsequent within the chemical and pharmaceutical trade, the place publicity to poisonous substances is a continuing problem, robotics performs an important position. Specialised robots geared up with subtle sensors and instruments function seamlessly in laboratories and manufacturing amenities. They conduct experiments, deal with hazardous supplies, and contribute to the precision and repeatability of vital processes, safeguarding human staff from potential hurt.
Whereas all of that is nice we should go over the challenges and measures related to robotics in hazardous environments:
- Robotic techniques should have strong designs the place they will face up to excessive circumstances, guaranteeing sturdiness and reliability.
- Working in distant and sophisticated settings requires progressive options for efficient communication.
- Meticulous danger assessments are performed to determine and deal with potential hazards.
- Growth of specialised robotic gear tailor-made to the distinctive challenges of hazardous environments.
- Incorporation of fail-safe mechanisms to deal with unexpected circumstances, guaranteeing each human and robotic security.
Synergies Amongst Traits
The intersection of assorted traits offers rise to unprecedented synergies, unlocking new potentialities and remodeling industries. The mixing of AI, IoT, and Superior Sensors creates an internet of interconnected applied sciences that empowers robotic techniques with heightened capabilities. AI enhances decision-making, IoT allows seamless communication between units, and superior sensors present real-time knowledge. This synergy kinds the spine of next-generation robotic functions.
The collaboration between AI and Robotics amplifies the adaptability and studying capabilities of robots. Machine Studying algorithms, fueled by huge datasets generated by sensors, allow robots to evolve and optimize their efficiency over time. Moreover, the wedding of IoT with Robotics enhances the effectivity of collaborative duties, permitting robots to speak and coordinate in dynamic environments.
Conclusion
In abstract, new developments in AI, machine studying, IoT, sensors, and collaborative applied sciences are propelling the fast evolution of the manufacturing facility robotics space. As seen, these developments are enabling extra versatile, self-governing, and networked robotic techniques, that are revolutionizing manufacturing processes.
As we speak, SMEs might reap the benefits of cost-effective and customizable options which can be personalized to satisfy their wants, in addition to specialised robots that safely deal with harmful duties. Robust synergies that improve capabilities are additionally unlocked by the convergence of various traits. Manufacturing is rising more and more versatile, efficient, and optimized as producers proceed to reap the benefits of these developments. Though there are nonetheless points with costs, safety, and scalability, the long run appears promising. Producers might absolutely make the most of robotics by conserving an in depth watch on progressive concepts and intentional cross-domain collaboration.
The long run factors to a brand new period of producing the place robotic applied sciences are integral companions in enhancing productiveness, security, and competitiveness throughout the trade.